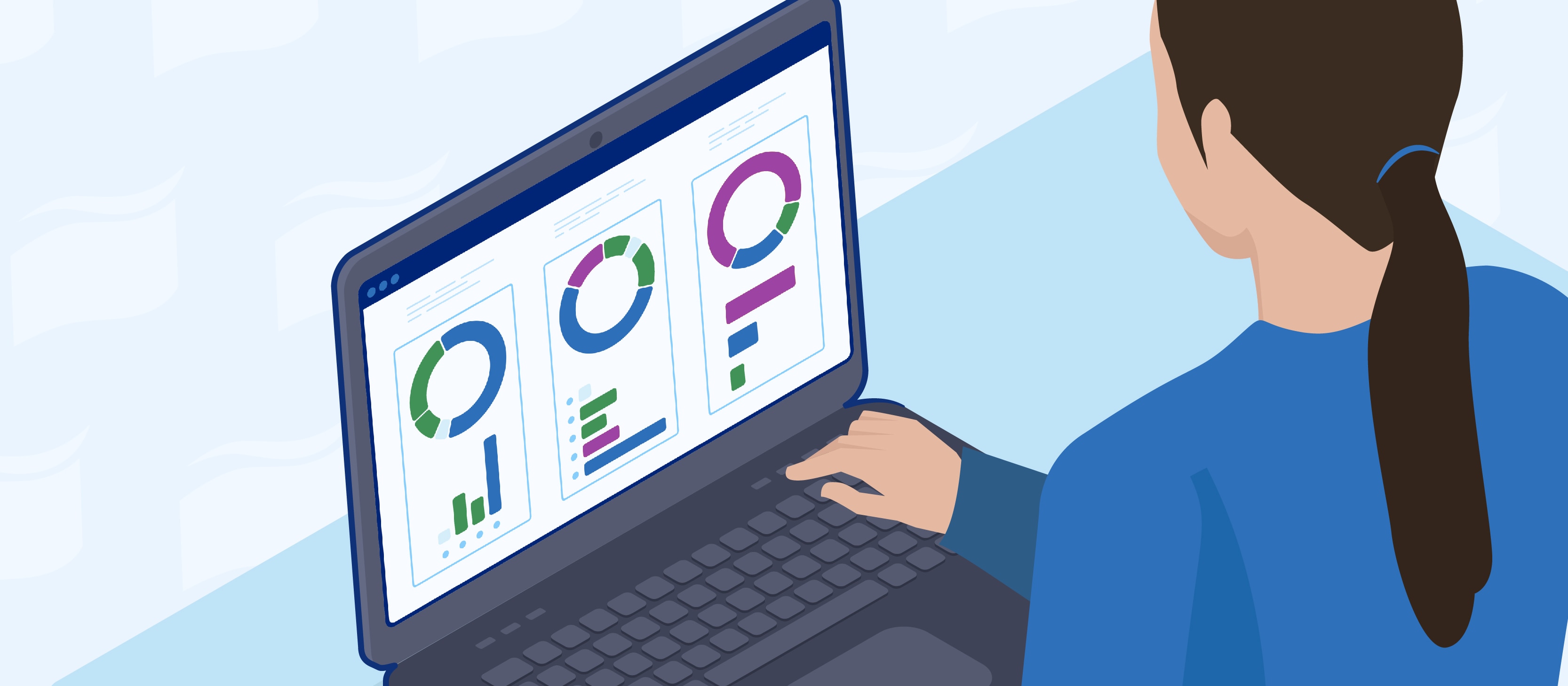
What is a Computerized Maintenance Management System? (CMMS)
Maintenance management is not an easy job. Doing it efficiently involves careful planning as well as making sure your business’s equipment, premises, and assets operate smoothly, minimizing downtime and potentially costly disruptions. The good news is, juggling all these moving parts gets easier by leveraging technology. Innovative tools like Computerized Maintenance Management Systems (CMMS) can help you handle your facility’s upkeep, track assets, and stay on top of repairs, all in one place. [1]
So, what exactly does a CMMS do and how can it be a valuable addition to your business? Let's take a closer look.
What does a Computerized Maintenance Management System (CMMS) do?
A CMMS offers a range of features designed to simplify maintenance management. Here’s a breakdown of the most common key functions that make it an essential tool for many businesses:
Asset & resource management
Most maintenance software helps you monitor in one place the use and availability of all the physical equipment, systems, and infrastructure that keep your facility operating. It usually holds detailed records of each asset, including its location, maintenance history, and performance, making it easier to plan for refills, repairs, or replacements.
Asset types that can usually be tracked in a CMMS include:
- Machinery and equipment
- Lighting and electrical systems
- Heating, ventilation, and air conditioning (HVAC) systems
Similarly, when it comes specifically to cleaning, facilities management software like Tork Vision Cleaning can take your operations to the next level. Our solution provides you with real-time data on restroom traffic and hygiene supply levels, helping your cleaning staff stay proactive. Features like smart sensors in your restrooms as well as dispensers and refill monitoring help ensure that resources are allocated where and when they’re needed most, boosting efficiency across your facility. The results speak for themselves: 7 in 10 cleaning managers say they improved efficiency in their operations with Tork Vision Cleaning.*
Work order management
Generally, with a CMMS, you can create and track work orders from start to finish. This type of software is designed to ensure duties are completed on time, with clear visibility of which critical tasks require immediate attention and which are done, streamlining your workflow.
Preventive maintenance
Scheduling regular maintenance is key to preventing equipment failure at your facility, and a CMMS can automate this process. It schedules tasks, sends reminders, and keeps track of when and how often upkeep is performed. Having a preventive maintenance program in place can reduce the risk of unexpected breakdowns or major repairs and even increase equipment lifespan.
Inventory management & distribution
A computerized maintenance management system commonly monitors equipment and supplies, helping you manage inventory levels efficiently and plan purchasing decisions. It alerts you when stock is low, ensuring you always have what you need on hand.
Taking the hospitality industry as an example, in hotels, tracking guest amenities such as shower products, linens, and mini-bar items helps prevent shortages. In restaurants and cafés, monitoring kitchen equipment can minimize downtime, while managing Serviceware like napkins or ingredients like condiments helps ensure seamless service during peak hours.
Regardless of your particular trade, monitoring stock of hygiene supplies like hand paper towels and hand soap is essential to promote health and safety in any facility. And it is just as important to ensure their efficient distribution across restrooms. Tork Vision Cleaning provides you with valuable features such as ‘Pack your trolley’, which helps cleaning staff know exactly which items to bring for each round. This boosts efficiency by reducing unnecessary trips back to storage areas, enabling your staff to maintain a clean, well-stocked environment. In fact, Tork Vision Cleaning makes sure that your dispensers are stocked 99% of the time**.
Reporting and analytics
Data-driven insights are crucial for maintenance optimization. A CMMS can help you better understand equipment performance, maintenance costs, and downtime, giving you the information you need to make informed business decisions and improve overall efficiency. This also eliminates the need for manual administrative tasks like creating reports. Plus, having computerized records takes away the risk of paper files getting lost.
What are the key components of a CMMS??
This kind of software is designed to bring maintenance operations together, making it easier for you to manage everything in one place. Let’s break down how such a system is typically structured.
Central database
The database stores all maintenance records and information, from equipment details to work orders and inventory. It tracks historical data and provides quick access to archives, helping you spot trends and improve your maintenance procedures and strategies.
User interface (UI)
The user interface allows maintenance staff and managers such as yourself to input data, manage work orders, schedule tasks, and view reports. It’s usually designed to be user-friendly and accessible from both desktop and mobile devices, making it easy for you to also work on the go. [2]
Integration with other systems
How can a CMMS benefit your business?
Increased efficiency and productivity
Cost-effectiveness
Improved data management
Who is responsible for a CMMS in your business?
Maintenance administrator
Maintenance manager/supervisor
References:
[1] https://www.ibm.com/topics/what-is-a-cmms
[2] https://www.linkedin.com/pulse/importance-user-friendly-cmms-interface-worktrek-njpef/
[3] https://mpulsesoftware.com/blog/cmms/who-should-manage-your-cmms-system-part-2/#